様々なニーズに
対応する
射出成形
プラスチック射出成形とは、プラスチック樹脂を加熱して溶かし、金型に射出することでプラスチック製品を作る方法です。金型を作ることで、複雑な形状や細かい形状の製品であっても短期間で大量に生産することが可能です。
長年の実績を持ち、開発力や技術力に優れた専門知識・経験豊富な技術者と、先進的な生産装置および生産技術を備えた充実した設備の総合力で、幅広いお客様のニーズに対応いたします。
小型から
大型製品まで
0.1g単位の細かな部品から最大約2.5kgの大型パーツまで、さまざまな大きさの射出成形に対応。難易度の高い形状も、プラスチック成形のプロによる技術でしっかりサポートいたします。
VA/VE提案
さまざまな課題を解決するVA/VE提案力が私たちの強みです。金属から樹脂化、ハイサイクルの実現、自動化への提案などでお客様のアイデアを形にして、コストメリットを提供します。
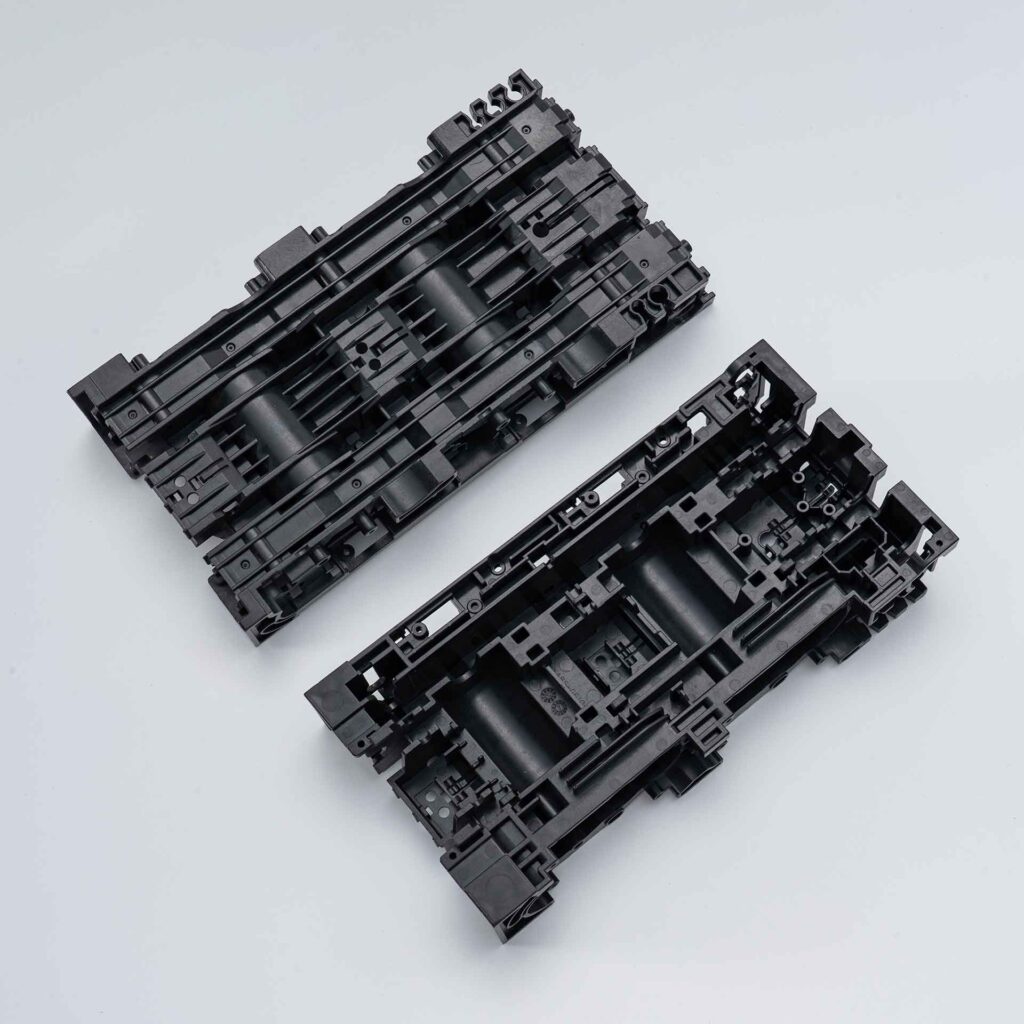
当社の強み
開発・技術力
VA提案や形状提案に自信があります。固有の金型技術を駆使し、変肉・肉厚・複雑形状の製品を高精度に成形します。
生産装置
工場を止めないための万全なインフラ。最新鋭の電動成形機83台と自動倉庫で、迅速な納期対応を可能にしています。
生産技術
組立装置の設計から設備の保守保全まで、すべて社内で一貫対応。様々なご要望に迅速かつ柔軟に対応します。
射出成形の主な流れ
01
樹脂を溶かす
ペレット状の材料をホッパーに投入。投入された材料がシリンダー内部で加熱され、内部が回転することで溶融した材料がシリンダーの先端へ送られていきます。
02
樹脂を金型に流し込む
シリンダーの先端を金型に押し付け、加熱されて溶けた材料を高圧で金型に流し込みます。材料の圧力で金型が開かないように強力に締め付けます。
03
圧力をかけて固める
金型に流した材料は金型の内部で冷やします。圧力を維持しながら材料が固まるのを待ちます。
04
製品の取り出し
製品が十分に固まったら、金型を開いてロボットで製品を取り出します。
製品化の流れ
01
受注・ディスカッション
お客様と機能や要件について協議をして、製品仕様、リードタイム、予算などの詳細を取り決め、より良いものづくりを目指します。
02
金型構造検討
製品仕様に基づく型構造(ゲート、ランナー、冷却回路、突き出し方法等)を検討。長年培ったノウハウを元に成形不具合を事前に推定して、対策を講じた金型構造(仕様書)を検討します。
03
金型製作
金型メーカーと金型構造について仕様書を元に設計打ち合わせ行い、金型レイアウト・組立図を確認して金型の製作を依頼します。
04
試作・測定
正常に成形ができるか試作を行います。金型作動が正常か、製品が設計通りか確認を行います。お客様が要求する形状や品質が
基準を満たすまで、必要な金型修正・試作を行います。
05
量産
試作結果良好、お客様の合格判定を頂いたのち、量産移行会議を実施し量産移管をいたします。
06
検査・品質管理
完成品が品質基準を満たしているか検査を行います。出荷検査で基準書基づき検査を行い、合格品の出荷許可をします。
07
出荷・納品
製品の出荷準備を行います。お客様のご注文に必要な数を準備し、納期に合わせてに配送行います。